Single-phase motor controls - 230 VAC
Fan speed controllers are used to control the speed of various kinds of electric fans, such as supply fans or exhaust fans used in ventilation systems. They reduce or increase fan speeds and thus slow down equipment wear and tear, decrease noise levels and save energy.
One possible option for regulation the speed of single-phase 230 VAC motors are transformer-based fan speed controllers. This particular type of controllers regulate the revolutions of the fan, i.e. its speed in predefined steps. As standard, Sentera’s controllers feature 5 steps.
How do I chose the correct type of fan speed controller?
The key aspect is compatibility. You need a controller that is fully compatible with your fan type, which means you must check the voltage and amperage requirements and any other specific features or refer to your motor characteristics. If your fan is equipped with an AC motor and what you want is a step-by-step fan regulation, Sentera’s fan speed controllers are a reasonable choice.
Transformer technology for fan speed control is the best-known method of reducing the supply voltage to a fan motor. Transformer based controllers are extremely dependable and minimise both the motor humming and buzzing, even at low motor speed, and the electromagnetic emissions, which are likely to upset sensitive electronic devices.
More than one fans can be controlled at the same time as long as the total amperage (i.e. maximum current) of all the connected motors does not exceed the maximum controller rating.

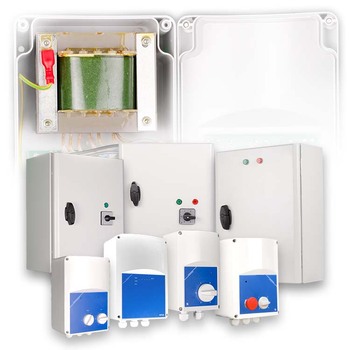
From the simplest manually operated controller through analogue input control to demand-based ventilation, these controllers offer a solution to fit any need.
Manually operated transformer fan speed controllers feature built-in knobs for speed adjustment depending on the occupant’s preferences.
For controlling a motor via an analogue input you need a 0 - 10 V control signal provided by an external device. This could be a sensor or an external potentiometer. If a potentiometer is connected, the control signal is sent manually by rotating the potentiometer. However, if a sensor is connected, ventilation could be based on its measurements, be it temperature, relative humidity, CO2 or any other parameter.
Temperature-based motor control is realized using a passive temperature probe connected to the controller. Naturally, not only do such controllers feature cooling and heating mode, but also manual and automatic mode. Automatic mode is based on the setpoint selected using a built-in potentiometer.
There are plug-and-play versions, in which both the connection cables and the temperature probes are connected. Additionally, there are versions with standard Euro sockets to connect the fans and heaters by simply plugging them in.
The controllers featuring calendar function have a built-in timer, thanks to which they can operate autonomously. Two optimal speeds can be selected and switched both manually via the built-in keyboard and automatically via the programmable timer functionality. Apart from being a standalone device, this type of controllers feature a USB port for connection to a computer. What you get is easy reading, changing and writing all device parameters via the free downloadable 3SMUsb software (part of 3SM Center).
The most advanced control type for 230 VAC motors using transformer technology is achieved by using Modbus RTU in place of the standard knob that is incorporated into the unit enclosure. Modbus operated controllers also features the so-called manual and automatic control mode. In manual mode, a BMS system or a Modbus RTU master device can be used to select the desired fan speed. In automatic mode, a Sentera HVAC sensor or SPV series of potentiometers can be used. Fan speed is controlled via the connected device. So, in automatic mode, fan speed can be controlled based on temperature, relative humidity, CO2, air quality (TVOC), CO, etc. measured by the connected sensor. If you go for the digital SPV potentiometer, you can control remotely using the potentiometer, while the transformer controller can remain in the technical room. These can also be controlled via a 0 - 10 Volt analogue input signal.