Differential pressure
Differential pressure is the difference in air pressure between two distinct points within an HVAC system. This pressure difference plays a crucial role in ensuring proper ventilation and air quality management for several reasons:
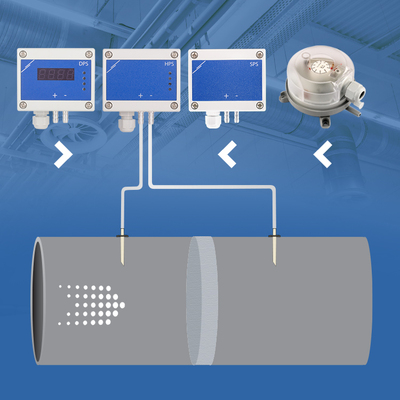
1. Airflow Control
Pressure differences drive airflow in buildings. By creating a pressure differential between two spaces, air moves from high-pressure areas to low-pressure areas, facilitating proper ventilation. This controlled movement helps in:
• Dilution of Contaminants: Fresh air is introduced and mixed with indoor air, diluting pollutants, odours, and CO2 levels, which improves indoor air quality.
• Exhaust of Pollutants: Contaminated or stale air is exhausted out of the building, maintaining a healthier indoor environment.
2. Preventing Airborne Contaminant Spread
Pressure differences help contain and control the spread of airborne contaminants, especially in critical environments like hospitals or laboratories. For instance:
• Negative Pressure Rooms: Used in hospitals to contain infectious agents by ensuring air flows into the room and not out into surrounding areas.
• Positive Pressure Rooms: Used in cleanrooms to keep contaminants out by ensuring air flows out of the room, preventing ingress of contaminants.
3. Thermal Comfort
Proper ventilation ensures a balance of temperature and humidity, contributing to occupant comfort. Pressure differentials can help manage this by:
• Balancing Temperatures: Ensuring that air is distributed evenly, preventing hot or cold spots.
• Humidity Control: Facilitating the removal of humid air and the introduction of drier air or vice versa, maintaining comfortable humidity levels.
4. Energy Efficiency
Managing pressure differentials is key to energy-efficient ventilation systems. Properly balanced systems reduce the workload on HVAC systems by:
• Optimizing Air Distribution: Minimizing the energy needed to move air throughout a building.
• Reducing Leakage: Ensuring that air moves only through intended pathways, reducing loss and improving system efficiency.
5. Building Integrity and Safety
Pressure differences can impact building integrity and safety by:
• Preventing Moisture Ingress: Controlling pressure can prevent moist outside air from infiltrating, which could cause mold growth and structural damage.
• Fire Safety: In smoke control systems, pressure differentials are used to prevent the spread of smoke in the event of a fire, aiding in safe evacuation and reducing fire damage.
Efficiently operating differential pressure sensors, controllers and switches are essential for achieving good air quality that every reliable HVAC system should create. Effective ventilation relies on maintaining the correct level of differential pressure throughout the system. Insufficient pressure differentials can lead to issues such as inadequate airflow, which compromises indoor air quality and comfort. Conversely, excessive differentials may strain components and increase energy consumption.
Sentera’s product range includes differential pressure switches, sensors and controllers.
How does a differential pressure switch work?
A differential pressure switch is an electro-mechanical device designed to detect a difference in pressure between two points.
These switches feature two ports linked to the respective pressure sources, thereby monitoring the differential pressure between them.
These switches feature two ports linked to the respective pressure sources, thereby monitoring the differential pressure between them.
When connected to two pressure sources, the differential pressure switch acts as an alarm to make or break a circuit as the pressure increases or decreases beyond the preset value.
Differential pressure switches can be used to realize energy savings or for preventative maintenance, for example; monitoring of air filters for clogs. If the filter has a blockage or clogging, the pressure on the high side will increase and once at the activation point, the pressure switch will change state.
How does a differential pressure sensor work?
A differential pressure sensor measures the difference in pressure between two points. It typically consists of two ports, one for high pressure and one for low pressure. The sensor measures the pressure at each port and calculates the difference between them. It finds applications in filter monitoring, cleanroom ventilation, etc.
The operational principle of a differential pressure sensor involves two hermetically sealed chambers, each equipped with a process connection. These chambers are separated by a flexible membrane, affixed with a resistance bridge. The process connections are positioned before and after any potential pressure reduction, ensuring that the pressures exert opposite forces on the membrane.
Under equal pressure conditions in both chambers, the membrane remains flat. However, when there is a variation in pressure within one of the chambers, the membrane deflects towards the chamber with the lower pressure. The extent of this deformation corresponds to the difference between the two pressures. This deformation induces a change in the resistance value of the bridge, which can then be converted into an electrical signal (transmitted by the sensor analogue output) for subsequent processing by an EC fan or AC fan speed controller.
Working Principle: The sensor has two ports that connect to different points in the HVAC system. The high port connects to the area of higher pressure, and the low port connects to the area of lower pressure. Inside the sensor, a diaphragm or membrane flexes when there is a pressure difference between the two ports. The amount of flex is proportional to the pressure difference.
The diaphragm movement affects attached strain gauges or piezoelectric elements, changing their electrical resistance or generating a voltage. This change is converted into an electrical signal (voltage, current, or frequency) proportional to the pressure difference. The processed signal is output as either an analogue signal (e.g., 0-20 mA, 0-10 V) or modulating signal (e.g. PWM or Modbus)
Integration with Control Systems: This output is fed into the HVAC control system, which uses the data to adjust fans, dampers, and other components to maintain desired pressure.
Sentera’s low-resolution sensor series utilize the piezoresistive effect, wherein the electrical resistance of a material changes under tension or pressure. A piezoresistive sensor is made from semiconductor. All piezoresistive sensors exhibit minimal drift. A piezoresistive sensor is made from semiconductor.
Sentera’s high-resolution sensor series feature a digital, low pressure MEMS sensor element (micro-electromechanical system) offering state-of-the-art pressure transducer technology and CMOS (complementary metal–oxide–semiconductor) mixed signal processing technology to produce a digital, fully conditioned, multi-order pressure and temperature compensated sensor with a dual vertical porting option. Micro-Electro-Mechanical Systems, or MEMS, is a technology defined by its miniaturized mechanical and electro-mechanical elements, created using microfabrication techniques. The physical dimensions of MEMS devices can range from well below one micron to several millimeters. These devices can be as simple as structures with no moving parts or as complex as electromechanical systems with multiple moving components controlled by integrated microelectronics. The defining feature of MEMS is the presence of elements with mechanical functionality, whether or not they move.
The key components of MEMS include miniaturized structures, sensors, actuators, and microelectronics, with the most notable being microsensors and microactuators. These elements are categorized as “transducers,” devices that convert energy from one form to another. Microsensors typically convert mechanical signals into electrical signals, making them critical in various applications.
How does a differential pressure controller work?
A sensor controller offers the possibility to define a setpoint for a single parameter. This setpoint is the greatest difference between this type of devices and the others. Instead of a range of values, only one point is acceptable for the sensor controller. This category contains only the Sentera's sensor controllers that measure differential pressure, volume flow and air velocity. It is a separate category because it does not have a proportional output, but a PI algorithm. PI stands for Proportional Integral. It is a control loop that continually calculates a correction between a setpoint and the actual measurement.
The PI algorithm controls the analogue output. The PI algorithm ensures that the controlled parameter retains its setpoint value.
The differential pressure controller controls the output to maintain the differential pressure at the requested setpoint.
A sensor controller offers the possibility to define a setpoint for a single parameter. This setpoint is the greatest difference between this type of devices and the others. Instead of a range of values, only one point is acceptable for the sensor controller. This category contains only the Sentera's sensor controllers that measure differential pressure, volume flow and air velocity. It is a separate category because it does not have a proportional output, but a PI algorithm. PI stands for Proportional Integral. It is a control loop that continually calculates a correction between a setpoint and the actual measurement.
The PI algorithm controls the analogue output. The PI algorithm ensures that the controlled parameter retains its setpoint value.
The differential pressure controller controls the output to maintain the differential pressure at the requested setpoint.
Sentera’s differential pressure sensors, switches and controllers are used to measure and control low differential pressures of non-aggressive and non-combustible gases, but they have been especially developed for air. The selectable analogue / modulating output signal has different meaning, depending on the setting of the device. If the device is used as a pressure sensor, the output signal is proportional to the measured pressure. As a volume flow sensor, the device calculates the process flow using differential pressure readings. In air velocity control, the output signal represents a manipulated variable of the PI control.
Depending on the connected differential pressure accessories, the devices can measure and/or monitor and control different parameters. Based on this measurement, air volume flow [m³/h] or air velocity [m/s] can be calculated. To calculate air volume flow based on the K-factor of the fan, use the connection set type PSET-PVC-200 or PSET-QF-200. This connection set can also be used to measure differential pressure. To calculate air volume flow based on the duct cross section [cm²] or air velocity [m/s], use the optional connection set type PSET-PTS-200 or PSET-PTL-200.
How does an air filter monitoring device work?
An air filter monitoring device is used to monitor the condition and efficiency of air filters. It employs sensors or detectors to assess factors such as airflow, pressure differentials, particle concentration, or filter resistance. By continuously monitoring these parameters, the device can indicate when filters need replacement or maintenance. This helps ensure that air filters are changed at the appropriate intervals, maximizing system performance, indoor air quality, and energy efficiency.
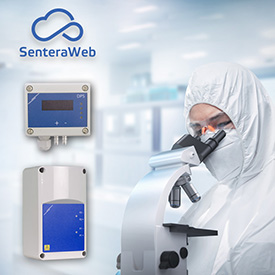
An air filter monitoring device is used to monitor the condition and efficiency of air filters. It employs sensors or detectors to assess factors such as airflow, pressure differentials, particle concentration, or filter resistance. By continuously monitoring these parameters, the device can indicate when filters need replacement or maintenance. This helps ensure that air filters are changed at the appropriate intervals, maximizing system performance, indoor air quality, and energy efficiency.
Sentera’s FIM series of filter monitoring devices, offers options to monitor either one or two air filters simultaneously. The series can be used for monitoring pressure drops.
Air filters impede airflow, creating resistance. As dust and particles accumulate, this resistance increases, causing a higher pressure drop across the filter. The monitoring device measures this pressure drop, indicating filter condition. If it surpasses a set threshold, it signals the need for maintenance.
Also, the FIM series can send real-time data and alerts, allowing continuous monitoring by operators or maintenance staff. Notifications or alarms are triggered when filters require attention, facilitating prompt maintenance actions. Alerts are delivered via SMS or email.
These devices record and store data on filter performance, pressure drop trends, and other relevant parameters. Analysis of this data enables identification of patterns, optimization of maintenance schedules, and detection of potential filtration system issues.
What is more, to facilitate the last two features, the FIM can be connected to SenteraWeb, our online HVAC portal, thanks to the integrated Sentera Internet Gateway.
Air filters impede airflow, creating resistance. As dust and particles accumulate, this resistance increases, causing a higher pressure drop across the filter. The monitoring device measures this pressure drop, indicating filter condition. If it surpasses a set threshold, it signals the need for maintenance.
Also, the FIM series can send real-time data and alerts, allowing continuous monitoring by operators or maintenance staff. Notifications or alarms are triggered when filters require attention, facilitating prompt maintenance actions. Alerts are delivered via SMS or email.
These devices record and store data on filter performance, pressure drop trends, and other relevant parameters. Analysis of this data enables identification of patterns, optimization of maintenance schedules, and detection of potential filtration system issues.
What is more, to facilitate the last two features, the FIM can be connected to SenteraWeb, our online HVAC portal, thanks to the integrated Sentera Internet Gateway.