What are the key components of an air handling unit?
The main parts of an air-handling unit (AHU) are shown on the drawing below. This picture will be used as an example; however, many other different combinations are possible.
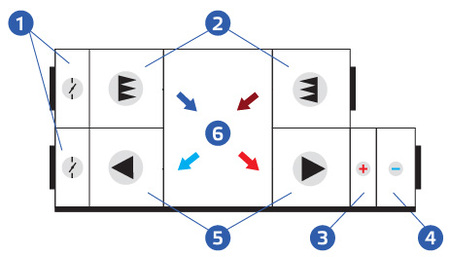
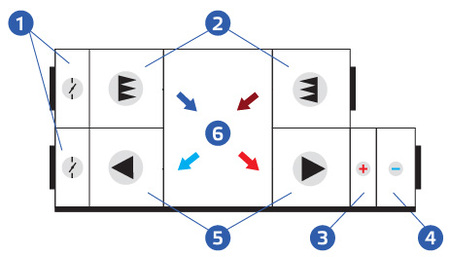
1. Air damper
The purpose of air dampers is regulating airflow. They are usually installed between air-handling unit and outside air. During the periods when the AHU is inactive, dampers prevent outside air from entering the unit. They create a barrier from dust, particles, leaves, insects and even small birds. Moreover, during the cold periods of the year, an air damper serves as frost protection for heating coils that use water. Air dampers are also a part of recirculation chambers and plate recuperators, which are described further in detail. Actuators control the position of dampers. Electric damper actuators are the most common type used for AHUs. They can be controlled by digital (on/off) signal, analogue signal (0-10V, 4-20mA) and via Modbus communication. Sentera offers a wide range of converters to implement electric dampers in the control solutions.
Damper with actuator
The purpose of air dampers is regulating airflow. They are usually installed between air-handling unit and outside air. During the periods when the AHU is inactive, dampers prevent outside air from entering the unit. They create a barrier from dust, particles, leaves, insects and even small birds. Moreover, during the cold periods of the year, an air damper serves as frost protection for heating coils that use water. Air dampers are also a part of recirculation chambers and plate recuperators, which are described further in detail. Actuators control the position of dampers. Electric damper actuators are the most common type used for AHUs. They can be controlled by digital (on/off) signal, analogue signal (0-10V, 4-20mA) and via Modbus communication. Sentera offers a wide range of converters to implement electric dampers in the control solutions.
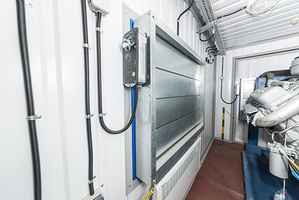
2. Filter
Generally, filters play a number of important roles within AHU and HVAC systems. According to European standards, there are 16 filter classes starting from G1 up to U16. Filter class is determined according to efficiency and particle size. The final choice of a filter depends on its application. Filters create healthy and comfortable environment for people as well as maintain suitable conditions for technological processes. Additionally, filters protect the air-handling unit itself because dust and other pollutants negatively affect the performance of the AHU parts and can even lead to their malfunction. Filters installed in exhaust AHUs prevent contamination of ambient environment. Monitoring the condition of filters is necessary for well-timed maintenance and sustaining overall system performance and efficiency. Specifically for that, Sentera offers a variety of differential pressure sensors and relays.
Filters
Generally, filters play a number of important roles within AHU and HVAC systems. According to European standards, there are 16 filter classes starting from G1 up to U16. Filter class is determined according to efficiency and particle size. The final choice of a filter depends on its application. Filters create healthy and comfortable environment for people as well as maintain suitable conditions for technological processes. Additionally, filters protect the air-handling unit itself because dust and other pollutants negatively affect the performance of the AHU parts and can even lead to their malfunction. Filters installed in exhaust AHUs prevent contamination of ambient environment. Monitoring the condition of filters is necessary for well-timed maintenance and sustaining overall system performance and efficiency. Specifically for that, Sentera offers a variety of differential pressure sensors and relays.
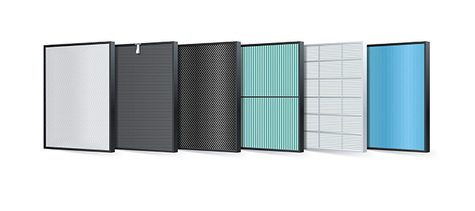
3. Heating coil
Heating coils are used to increase the temperature of supplied air. In terms of energy source, there are four main different types of heating coils: liquid, electric, steam and gas heating coils. Liquid and electric heaters are used in most cases, while steam and gas heating coils are widely applicable in plants and industrial facilities where steam or gas is utilized during manufacturing processes.
Apart from different energy source, liquid and electric heating coils require their own control equipment.
Control equipment for liquid heater include: pump, valve, temperature sensors and thermostat. The pump creates liquid flow through the system, while the actuator controlled valve regulates the amount of media supplied to the heating coil. Readings from a duct temperature sensor are transferred to an HVAC controller to define the position of the valve. Surface-mounted temperature sensors and frost protection thermostats are safety devices which prevent liquid from freezing inside the tubes. You can easily integrate external equipment by using Sentera converters. Moreover, frequency inverters will provide variable speed control for the pump.
Heater
Heating coils are used to increase the temperature of supplied air. In terms of energy source, there are four main different types of heating coils: liquid, electric, steam and gas heating coils. Liquid and electric heaters are used in most cases, while steam and gas heating coils are widely applicable in plants and industrial facilities where steam or gas is utilized during manufacturing processes.
Apart from different energy source, liquid and electric heating coils require their own control equipment.
Control equipment for liquid heater include: pump, valve, temperature sensors and thermostat. The pump creates liquid flow through the system, while the actuator controlled valve regulates the amount of media supplied to the heating coil. Readings from a duct temperature sensor are transferred to an HVAC controller to define the position of the valve. Surface-mounted temperature sensors and frost protection thermostats are safety devices which prevent liquid from freezing inside the tubes. You can easily integrate external equipment by using Sentera converters. Moreover, frequency inverters will provide variable speed control for the pump.
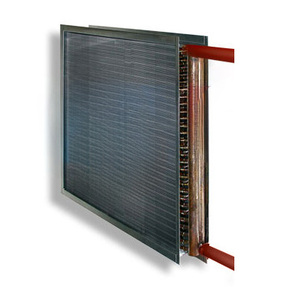
Electric heaters are controlled according to the readings from a duct temperature sensor. The majority of heaters have more than one power step. They are activated and deactivated via digital or analogue signal. Moreover, most electric heaters have a special built-in relay for overheating protection. Sentera offers a variety of converters to use all of the features mentioned above within your control solution.
4. Cooling coils
Coiling coils are used to decrease the temperature of supplied air. There are two main different types of coolers: liquid and direct expansion (DX) coolers, also known as evaporators. The choice of a liquid cooler depends on customer needs and the specifics of their HVAC system.
Control equipment for cooling coils has its own unique features.
Both coil types operate according to a duct or room sensor. Most of our temperature sensors measure relative humidity, too. This can be useful if a cooling coil is designed to operate as a dehumidifier.
Additional control equipment for liquid coolers also involves a two- or three-way valve. An electric actuator defines the position of the valve, making it possible to adjust cooling media flow to the coil. Another vital part of cooling systems is a chiller which provides media to coil.
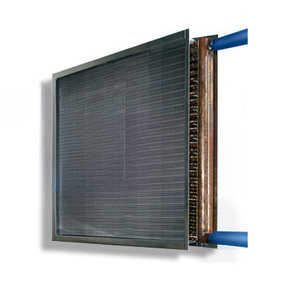
DX-cooler utilizes an expansion valve - a device that controls the amount of refrigerant released into the evaporator. There are two types of expansion valves: thermal and electric valves. Thermal expansion valves dynamically adjust the flow of refrigerant according to the temperature of the refrigerant that leaves the evaporator. They do not have any wiring. Electric expansion valves, on the contrary, need to receive signal from a special controller, usually integrated in the automation system of a compressor-condenser unit, a compulsory part of cooling systems.
DX-cooler
To sum up, all mentioned equipment for cooling coils could be integrated in a Sentera control solution.
5. Fan
Undoubtedly, a fan is the most important part of AHUs and ventilation systems. Fans create airflow and distribute it through ducts to or from a served area. Fans consist of two main parts – an impeller and a motor. Auxiliary components include gears, belts and pulleys, casings and many more. The motor is of great importance because it is a controllable power source for the fan. There are two types of motors commonly used with fans in AHU – AC and EC. Sentera offers control equipment for both motor types: electronic and transformer fan speed controllers as well as frequency inverters are compatible with AC fans, whereas EC fans work with control switches and potentiometers.
EC fan
AC fan
-cooler.jpg)
To sum up, all mentioned equipment for cooling coils could be integrated in a Sentera control solution.
5. Fan
Undoubtedly, a fan is the most important part of AHUs and ventilation systems. Fans create airflow and distribute it through ducts to or from a served area. Fans consist of two main parts – an impeller and a motor. Auxiliary components include gears, belts and pulleys, casings and many more. The motor is of great importance because it is a controllable power source for the fan. There are two types of motors commonly used with fans in AHU – AC and EC. Sentera offers control equipment for both motor types: electronic and transformer fan speed controllers as well as frequency inverters are compatible with AC fans, whereas EC fans work with control switches and potentiometers.
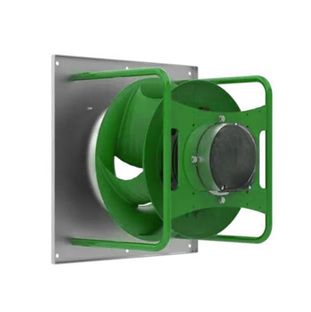

6. Energy recovery unit and recirculation chamber
Air-to-air energy recovery heat exchangers were found in the second half of 20th century. Since then their role in heating, ventilation and air conditioning (HVAC) industry has increased dramatically. The reasons are the constant rise of energy prices and tightening standards. There are three main types of energy recovery units: a plate recuperator, a rotary recuperator and a liquid-coupled heat exchanger. In addition, recirculation chambers are also considered as a way of energy exchange between supply and exhaust airflows. These methods have different efficiency, application area and control principles, as well as auxiliary automation equipment. Check out our AHU solutions section for additional information.
Air-to-air energy recovery heat exchangers were found in the second half of 20th century. Since then their role in heating, ventilation and air conditioning (HVAC) industry has increased dramatically. The reasons are the constant rise of energy prices and tightening standards. There are three main types of energy recovery units: a plate recuperator, a rotary recuperator and a liquid-coupled heat exchanger. In addition, recirculation chambers are also considered as a way of energy exchange between supply and exhaust airflows. These methods have different efficiency, application area and control principles, as well as auxiliary automation equipment. Check out our AHU solutions section for additional information.
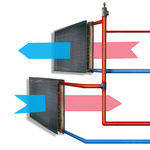
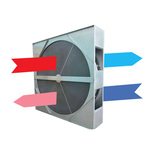
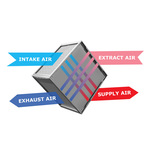
Conclusion
Understanding the key components of an AHU is essential for proper designing and optimizing of HVAC performance. Each of these components plays a crucial role in ensuring that the system operates efficiently, maintains air quality and meets the specific needs of the space it serves.
As a manufacturer of advanced control solutions for AHUs, Sentera is committed to enhancing the functionality and efficiency of your HVAC system.
Understanding the key components of an AHU is essential for proper designing and optimizing of HVAC performance. Each of these components plays a crucial role in ensuring that the system operates efficiently, maintains air quality and meets the specific needs of the space it serves.
As a manufacturer of advanced control solutions for AHUs, Sentera is committed to enhancing the functionality and efficiency of your HVAC system.